Producing hydrogen at sea | Why ships could soon be powered by recycled soda cans, coffee grounds and seawater
Reaction discovered by MIT researchers when ‘playing around’ in the lab could remove the need for marine vessels to carry massive onboard tanks filled with hydrogen, ammonia or methanol
Decarbonising the worldwide shipping industry — which produces about 3% of global greenhouse gas emissions — may prve to be one of the toughest tasks on the road to achieving net-zero emissions.
Tens of thousands of vessels will need to switch from using fossil fuels to biofuels or green hydrogen-based fuel — with green ammonia or methanol currently being touted as the most likely solutions, which would require gargantuan amounts of money and renewable energy.
But what if the hydrogen could be produced onboard without the need for renewable energy, using inexpensive waste materials?
Researchers at the prestigious Massachusetts Institute of Technology (MIT) in Boston believe they may have found such a solution — one that was discovered when they were “playing about” in the lab.
It has long been known that when pure aluminium (known as “aluminum” in the US] that has not been contaminated by oxygen in the air comes into contact with water, a chemical reaction occurs that produces hydrogen gas, heat and a type of aluminium oxide.
The researchers found that this reaction also worked using seawater, but that it was a pretty slow reaction.
“On a lark, they tossed into the mix some coffee grounds [the remains of coffee beans leftover after brewing coffee] and found, to their surprise, that the reaction picked up its pace,” explained an MIT press release.
“In the end, the team discovered that a low concentration of imidazole — an active ingredient in caffeine — is enough to significantly speed up the reaction, producing the same amount of hydrogen in just five minutes, compared to two hours without the added stimulant.”
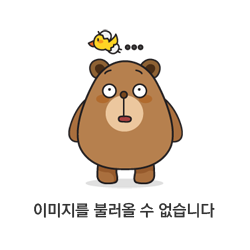
Kombargi (left) and fellow researcher Niko Tsakiris (right) working on a new hydrogen reactor that will be able tp produce hydrogen gas from aluminium and seawater at sea.Photo: MIT
PhD student Aly Kombargi, who is the lead author on the resulting study, explained: “We were just playing around with things in the kitchen, and found that when we added coffee grounds into seawater and dropped aluminum pellets in, the reaction was quite fast compared to just seawater.”
However, the aluminium-water reaction comes with a “sort of Catch-22”, the university explained, as the metal forms a “shield-like layer” of oxide as soon as it comes into contact with oxygen in the air — which is why aluminium soda cans do not react with H2O.
“In previous work [in 2021], using fresh water, the team found they could pierce aluminum’s shield and keep the reaction with water going by pretreating the aluminum with a small amount of rare metal alloy made from a specific concentration of gallium and indium. The alloy serves as an ‘activator’, scrubbing away any oxide build-up and creating a pure aluminum surface that is free to react with water.”
The researchers estimate that 1g of recycled-aluminium pellets would generate 1.3 litres (0.09g) of hydrogen in five seconds. In other words, roughly 9.3kg of aluminium would be required to produce 1kg of H2.
But in order to make the process sustainable and affordable, the researchers needed to find a way of recovering and recycling the expensive gallium indium (GaIn).
They found that ions (atoms or molecules with an electrical charge) protected the GaIn from reacting with the water and helped it “precipitate into a form that can be scooped out and reused”.
“Lucky for us, seawater is an ionic solution that is very cheap and available,” said Kombargi, who tested the idea with seawater from a nearby Boston beach. “I literally went to Revere Beach with a friend and we grabbed our bottles and filled them, and then I just filtered out algae and sand, added aluminum to it, and it worked with the same consistent results.”
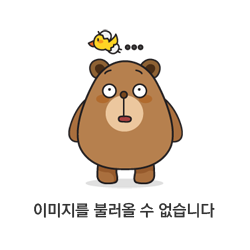
A researcher protects aluminum pellets from the air by dipping them in a mixture of gallium-indium.Photo: MIT
Even the waste product from the process — aluminium oxyhydroxide (also known as boehmite) — is a valuable commodity that can be collected and sold for use in a wide range of industries — including as a coating material that enhances the thermal and mechanical stability of electric vehicle batteries, as a flame retardant in plastics and electronics, and as a strengthening material in ceramics. Selling this mineral would help to lower the costs of hydrogen production.
The research team — led by mechanical engineering professor Douglas Hart — is now developing a small reactor that could run on a ship or submarine.
“The vessel would hold a supply of aluminum pellets (recycled from old soda cans and other aluminum products), along with a small amount of gallium-indium and caffeine,” MIT explained in the press release.
“These ingredients could be periodically funneled into the reactor, along with some of the surrounding seawater, to produce hydrogen on demand. The hydrogen could then fuel an onboard engine to drive a motor or generate electricity to power the ship.”
Kombargi added: “This is very interesting for maritime applications like boats or underwater vehicles because you wouldn’t have to carry around seawater — it’s readily available. We also don’t have to carry a tank of hydrogen. Instead, we would transport aluminum as the ‘fuel,’ and just add water to produce the hydrogen that we need.”
The researchers — who have published their findings in the Cell Reports Physical Science journal — did not, however, say how much the resulting hydrogen would cost to produce, merely stating at the end of their study: “The carbon footprint and overall cost of the process are subjects of ongoing analysis, with plans for a detailed life cycle analysis and further economic evaluations in upcoming studies.
“These assessments are essential to determine the sustainability and economic viability of this technology.”
Pennsylvania-based start-up GenHydro — which Hydrogen Insight interviewed back in October 2022 — is also working on producing hydrogen from scrap aluminium.
Source:Hydrogeninsight