電動パワトレに進化の余地 コスト1/3、トヨタ「次の一手」は熱マネか
2代目となったトヨタ自動車の燃料電池車(FCV)「MIRAI(ミライ)」。燃料電池(FC)システムを刷新し、「コスト半減」という至上命題を達成した。ハイブリッド車(HEV)との部品共通化を進める中では、熱の扱いに奮闘。今後は、「bZ4X」など次世代の電気自動車(EV)との連動が重要になりそうだ。
世代ごとにシステムコストを半減する―。トヨタがHEVで課してきた鉄の掟(おきて)だ。「普及してこその環境車」を標榜するトヨタとしては、この掟はFCVでも必達目標となる。2代続けてミライの開発責任者を務めた田中義和氏(トヨタMid-size Vehicle Companyチーフエンジニア)は「初代からコストを半分以下にできた」と胸を張る。
トヨタによると、燃料電池(FC)スタックや水素タンク、補器類などを含めたFCシステム全体のコストは、初代比で1/3に低減したという。大幅なコスト低減に向けて同社が打った手は、(1)専用部品の構造簡素化や量産性向上と(2)HEVとの部品共通化の2つである。
白金だけで10万円以上のコスト削減
FC専用部品の多くは、フロントフード下に配置した(図1)。コスト削減に特に効いたのが、発電を担うFCスタックである。分かりやすいのが、FCスタックのセル数である(表)。最高出力を初代の114kWから128kWに高めつつ、セル数を370枚から330枚に減らした。これで、セルを積み重ねる工程を40枚分少なくできた。性能を犠牲にしているわけではなく、体積出力密度で比較すると3.5kW/Lから5.4kW/Lに高めている。
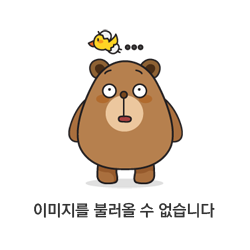
車種 | 初代ミライ | 2代目ミライ | |
2014年 | 2020年 | ||
3.5kW/L | 5.4kW/L | ||
370枚 | 330枚 | ||
114kW | 128kW | ||
2本 | 3本 | ||
4.6kg | 5.6kg | ||
113kW | 134kW | ||
335N・m | 300N・m |
セル単体の構造も見直した。セルは、水素と空気中の酸素を反応させるMEA(Membrane Electrode Assembly、膜電極接合体)を、水素と空気の流路(ガス流路)を成形したセパレーターで挟んで構成する。
新型ミライのセルは、セパレーターの数を従来の3枚から2枚に減らした(図2)。削減したのは空気極側。初代は2枚のチタン(Ti)製のセパレーターを使った。新型セルは「1枚のTi製セパレーターで同等の空気の拡散性を実現できる構造にした」(田中氏)という。
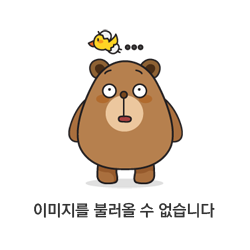
MEAの触媒層に使う白金(Pt)の量も大幅に減らした。堀場製作所の協力を得て新型ミライのFCセルを分析したところ、FCシステム1台当たり約19.2gのPtが使われていることが分かった。Ptの使用量についてトヨタは「初代から58%低減」と説明しており、初代ミライでは約45.7gのPtを使用していたと計算できる。現時点でのPtの価格は約4000円/gで、MEAだけで車両1台当たり10万円以上のコストを低減したことになる。
水素タンクも刷新した。まず、70MPa以上の高圧水素に耐えられる強度を確保する役割を担うCFRP(炭素繊維強化樹脂)層を見直した。タンクは、樹脂ライナーと呼ばれる水素ガスの貯蔵容器にCFRPを巻き付ける構造である。
今回、CFRPの巻き方の変更によって強度を向上させた。初代ミライに搭載した水素タンクはCFRPを27層重ねていたが、今回は25層に減らせた。CFRP層を薄くしたことで、水素の貯蔵性能が上がった。
トヨタの開発担当者によると、「CFRPの巻き方を変えることで生産性を3倍に高めた」という。さらに、搭載する3本の水素タンクの直径を揃えることで、タンクの製造装置を統一した。CFRPの巻き方をはじめとするタンクの設計・開発費も抑制できたようだ。
昇圧コンバーターがつなぎ役
FC専用部品の中で異色なのが、FCスタックの上に重ねて配置した昇圧コンバーターである。FCスタックで発電した電力を昇圧する部品だが、肝は650Vまで高める点にある。FCスタックで発電した電力は300Vほど。これを650Vまで高めるのは、トヨタのハイブリッドシステムと電圧を揃えるため。これで、既存のハイブリッド車(HEV)向け部品を流用できるようになった。
昇圧コンバーターはSiC(炭化ケイ素)のパワー半導体素子を採用するなどコストがかかっている。それでも、つなぎ役として昇圧コンバーターを追加したほうがシステム全体では安く済むとトヨタは判断した。
発電した電力を蓄えるリチウムイオン電池は「レクサスLS」のHEVと同じだった。PCU(パワー・コントロール・ユニット)はトヨタのHEVで広く使われているものだ。
駆動モーターはトヨタのFR(前部エンジン・後輪駆動)のHEVから流用したが、ひと手間加える必要があった。冷却機能の追加だ。モーターとエンジンを積むHEVの場合、高速走行中はエンジンが駆動力を生み出す中心になる。モーターは回転数が上がると効率が落ちるためだ。過熱は劣化にもつながる。
HEVとは異なり、駆動源としてモーターしか持たないFCVは、高速走行時でもモーターを休ませることはできない。そこでトヨタは、熱対策として駆動モーター専用のオイルクーラーを2個も用意した(図3)。この冷却系は後輪駆動ユニットのみで独立していた。
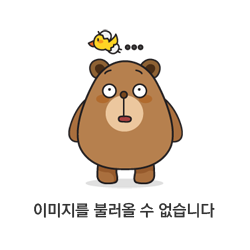
次の一手は熱マネの統合か
熱対策では、FC専用部品でも奮闘の痕跡が残った。フロントフード下から取り出したFCシステムに、さまざまな配管が張り巡らされていたのだ(図4)。

FCスタックとつながる配管を調べると、無色透明な液体が出てきた。スタックを温度調整する冷却液(クーラント)だ。電極間を流すため、絶縁性のあるクーラントを選択した。FCスタックの上に配置した昇圧コンバーターには別のクーラントが流れる。赤色のもので、昇圧コンバーターやPCUを冷やす。
クーラントを放熱するラジエーターはフロントグリル内にあり、3層構造の大掛かりなものだった(図5)。2種類のクーラント用のラジエーターに加えて、エアコン用のコンデンサーを並べた。

熱マネジメントは、電動車両における重要な競争軸になってきた。電池やモーター、FCスタックなど最適に温度管理しつつ、システム全体で効率的に熱を融通することが商品力の向上に直結する。
電動車両の熱マネジメントを巡っては、米Tesla(テスラ)を筆頭に統合化へと進む。ドイツVolkswagen(フォルクスワーゲン)も追従する姿勢を、量販EV「ID.3」の分解調査で確認した。電動車両の効率改善やコストの更なる低減に向けて、トヨタも統合型熱マネジメントシステムの導入が必要になるだろう。
注目すべきは、22年内に発売予定のEV「bZ4X」。トヨタでEV開発を主導する豊島浩二氏(トヨタZEVファクトリー チーフエンジニア)は、「bZ4Xは各種熱マネジメント技術を駆使して省エネ化を図った」と明かす。
今回分解したミライの熱マネジメントシステムは、FCシステムと駆動系で分断されていた。次期FCVで統合化を進めることが、「世代ごとにシステムコスト半減」という至上命題を達成する重要なポイントになりそうだ。
'Fuel Cell' 카테고리의 다른 글
ホンダのFCV用エンジンと可搬型汎用電源ユニット…水素・燃料電池展2022 (1) | 2022.03.21 |
---|---|
Honda to power its US HQ data center with 1MW fuel cell system (0) | 2022.03.21 |
分解調査で分かった、トヨタFCV「ミライ」の主要部品 (0) | 2022.03.17 |
トヨタは電池をどう冷やす? 「ミライ」分解で見えた風の流れ (0) | 2022.03.17 |
KR, Daewoo and STX Join Forces to Work on Solid Oxide Fuel Cells for Ships (0) | 2022.03.04 |