Hydrogen Contango’s new CCM- Make PEM water electrolyser’s price 150 €/kW happen
The hydrogen economy is on the brink of a revolution. Among the various electrolysis technologies, Proton Exchange Membrane (PEM) water electrolysis stands out for its efficiency and versatility, paving the way for a sustainable future.
However, the route to widespread adoption has not been without its challenges. The cost of PEM electrolysers has been a topic of intensive research and development. A report from IRENA suggests that the cost of electrolyser stacks, a critical component of PEM electrolysers, could be reduced to between 63–234€/kW for PEM by 2030, down from 384–1071€/kW in 2020, respectively. Also, the U.S. Department of Energy (DOE) has set ambitious targets for PEM electrolysis, aiming for a significant reduction in costs of PEM water electrolysis to 100$/kW (90€/kW) in 2026.
Hydrogen Contango is a Singapore based company at the forefront of innovation in the PEM water electrolysis field. As a part of the Hydrogen Age, they are leading in themanufacturing technology of catalyst and CCM, through years of research in the field of PEM water electrolysis.
Due to their newest 4th Generation Hydrogen Crossover Control Technology - Xiange Layer, which can supply onto the 50μm membrane. This made their CCM can achieve 1.8V under conditions of 4A/cm2 at the temperature of 60°C. Moreover, the hydrogen production efficiency reaches over an impressive 97%. Even under this amazing performance, the CCM still maintains high stability, exhibiting a minimal voltage decay of less than 10μV per hour. In addition, there is excellent improvement in hydrogen crossover rate which is less than 0.3% in oxygen at a current of 0.2A with bias pressure of 3MPa.
By applying Contango's 4th Generation Hydrogen Crossover Control Technology to a Nafion N115-based or 80μm membrane-based MEA, the PEM water electrolysis system will be capable of maintaining a stable internal bias pressure during halts for some period, even when the input electricity load drops to as low as 1% or lower. This provides a significant advantage when the electricity input comes from highly fluctuating sources, such as wind or solar PV plants. As a result, this technology helps reduce overall operational costs and enhances the economic viability of green hydrogen production.
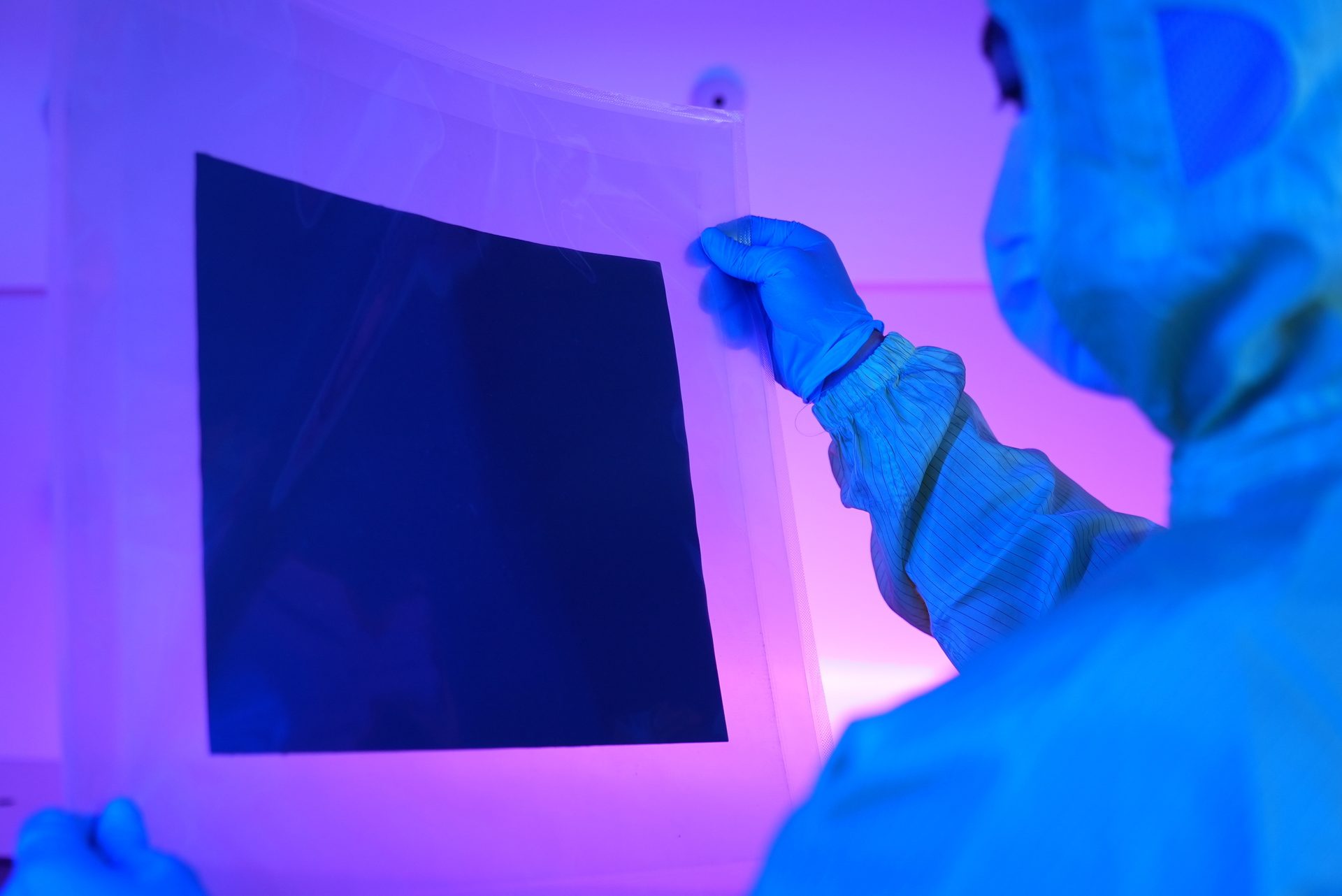
Proton Exchange Membrane Catalyst Coated Membrane
Photo: Hydrogen Contango
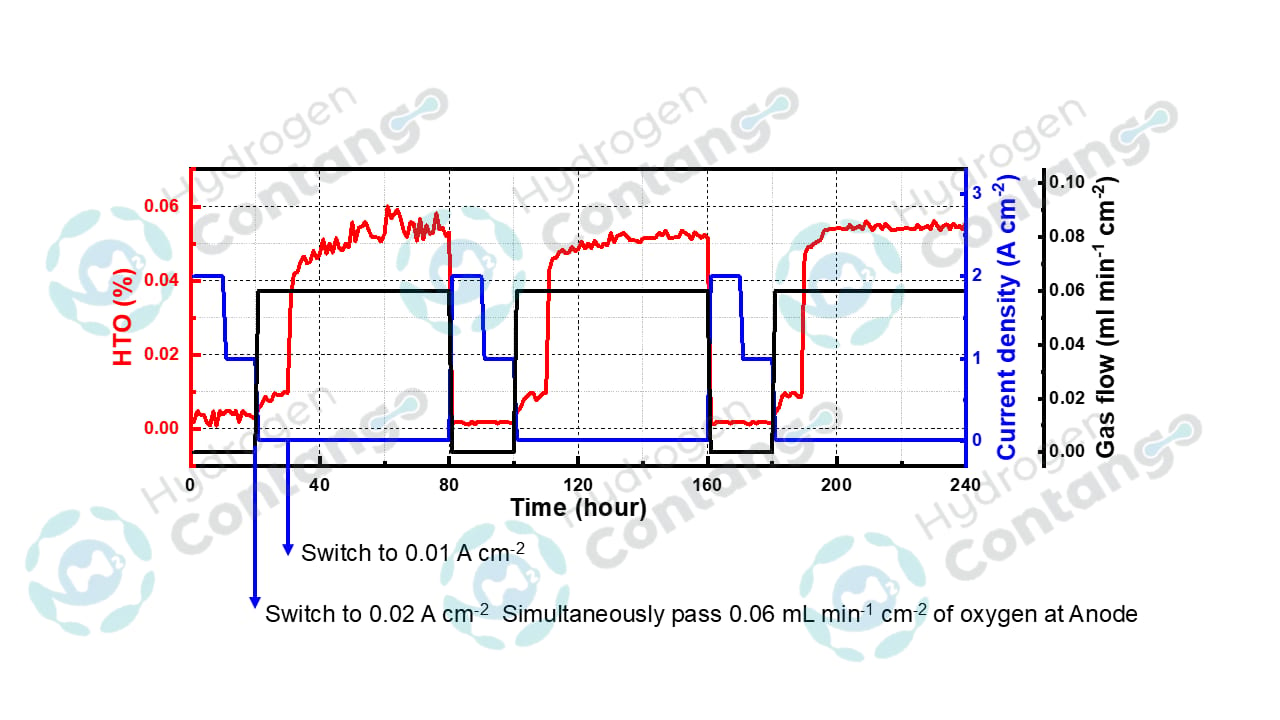
Test data of ultra-low input loading (near 0%) operating condition (Data: Hydrogen Contango)
Photo: Hydrogen Contango
Their latest breakthrough sees the company bring the cost of PEM water electrolysis down to an unprecedented price of 150€/kW. This achievement is not just a number on a spreadsheet, but also accelerating the transition to a greener, more sustainable future.
Contango's advanced CCM manufacturing capabilities now extend to a maximum 1 metre in width, offering unlimited length options, and are fully customisable to client specifications.
“We're fuelling the future with unwavering dedication to PEM technology. Together, let's charge towards a hydrogen-empowered world!” - Nathan Wang, CEO
They will be at Booth A4 4F48 during the Hydrogen Technology & Carbon Capture Expo 2024 Hamburg, October 23-24.