New £1.5M UK-Taiwan Initiative Targets Next-Gen Hydrogen Production with Bramble Energy’s Breakthrough Electrolyser Technology
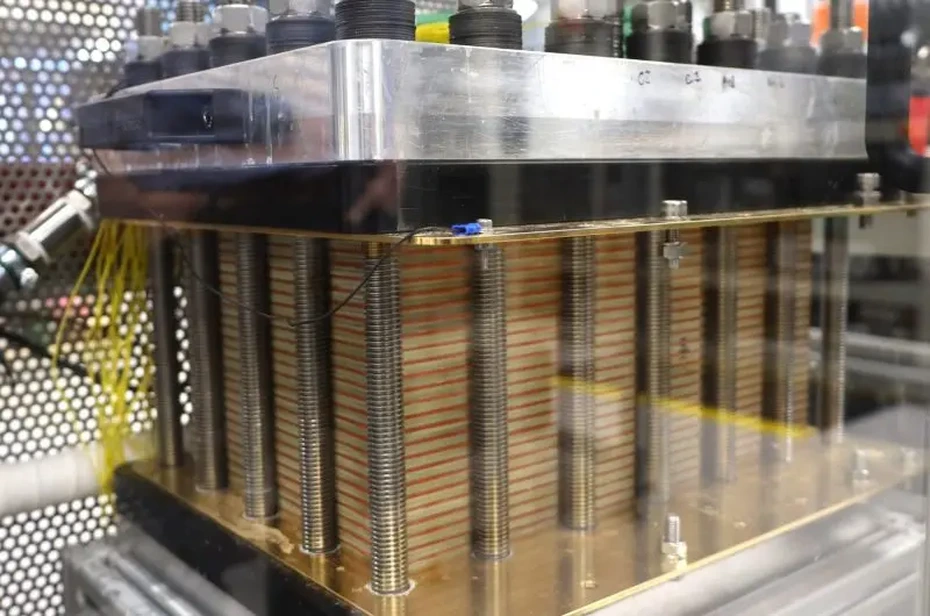
Bramble Energy
London, UK.-- UK cleantech specialist Bramble Energy, in partnership with Taiwan-based Tripod Technology Corporation and Tripod Nanotechnology Corporation, today announces the launch of a £1.5m ‘POWER project’ – an initiative set to develop Bramble’s patented Printed Circuit Board AEM Electrolyser (PCBEL™) and redefine the economics and scalability of hydrogen production.
Co-funded by Innovate UK and Taiwan’s Department of Industrial Technology via the UK-Taiwan CRD 2024 program, the project – named ‘POWER: Printed Circuit Board Optimised Water Electrolysis with Reduced Platinum Group Metals (PGM)’ – builds on the success of Bramble’s existing PCBEL™ stack technology.
Key milestones so far include demonstrating it in a 25 kW stack, operating on just 0.1 mol/L KOH (potassium hydroxide solution) – a significantly less corrosive concentration that simplifies handling, reduces stringent safety requirements, and enables a broader range of material choices. PCBEL™ has also achieved the Clean Hydrogen Partnership’s 2030 targets for performance and critical raw material (CRM) content, and it leverages the high-volume, low-cost printed circuit board (PCB) supply chain, which has reached an industry-leading volume cost of $200/kW for AEM stacks.
Within the project, Bramble Energy and its partners will refine the PCBEL™ cell and stack design, while integrating breakthrough catalysts and developing membrane electrode assemblies (MEA).
The result will see the cost of AEM electrolyser stacks further lowered by improving durability and operational flexibility.
“We are thrilled to announce this £1.5m project to develop our groundbreaking PCBEL™ technology,” said Dr Tom Mason, CEO of Bramble Energy. “This is more than just an upgrade in technology; by combining cutting-edge engineering with a commitment to affordability and sustainability, we’ll be able to push the limits of cost, performance and durability, propelling our electrolyser technology towards large-scale commercialisation. Being able to deliver a low-cost, scalable and reduced precious-metal solution to hydrogen production will be an exciting turning point for the entire hydrogen economy, helping drive the transition to a clean energy future.”
Aleck Lin – Vice President of Tripod Technology added
“As a global leader in PCB manufacturing, Tripod Technology is excited to join in this PCB-based pioneering project of advanced AEM electrolyzer development. In the international collaborative project, Tripod and Tripod Nano are dedicated to innovating catalyst and membrane electrode technology for better performance and material sustainability. This partnership with Bramble underscores our commitment to technological leadership and global decarbonization, ensuring stable and scalable material supply for the clean energy transition.”
As governments and industries worldwide seek robust solutions to decarbonise critical sectors, the POWER project positions the consortium at the forefront of the next-generation AEM electrolyser market, while paving the way for a resilient, sustainable energy infrastructure that can meet the demands of tomorrow.
For more information about Bramble Energy, visit https://www.brambleenergy.com/.
About Bramble Energy
Bramble Energy is an award-winning cleantech business accelerating global decarbonisation and powering the transition to a Net Zero world.
Backed to date with £41 million from prominent investors HydrogenOne Capital, Parkwalk Advisors, UCL Technology Fund, BGF and IP Group, Bramble Energy continues to grow its team, technologies and facilities.
Bramble Energy was the recipient of “Business Transformation of the Year Award” at The Lloyds Bank British Business Excellence 2023 Awards, was placed in Deloitte’s EMEA Fast 500 ranking, and announced as the Deloitte UK Fast 50 Regional winner of the South East.
Founder Dr Tom Mason has grown a team of three in the research labs at University College of London to an 80+ strong team of experts across electrochemistry and high impact technological solutions.
Headquartered in Crawley, UK, Bramble Energy is based in a multi-million pound world-leading hydrogen innovation hub, enabling the company to push the boundaries and scale-up its technologies to solve the global challenge of making clean energy technology accessible. Focusing on manufacturability, scalability and rapid innovation, the company has developed PCB-X™ – a versatile hydrogen platform that leverages printed circuit board (PCB) technology to create a series of patent protected clean energy solutions. These include the PCB fuel cell, PCBFC™, which uses globally standardised materials and manufacturing techniques, enabling low cost local production and scalability, and PCB electrolysers, which are accessible, stackable and low cost.
About Tripod Technology Corporation
Founded in 1991, Tripod Technology Corporation is a world-class PCB manufacturer with state-of-the-art production facilities in Pingzhen, Taoyuan, Taiwan. With operations spanning 12 countries and 19 cities, Tripod provides precision multilayer PCB manufacturing, reliable delivery schedules, and cost-effective solutions to a global customer base.
As part of its commitment to continuous innovation, Tripod began the development of hydrogen production equipment in 2023, expanding its technological expertise beyond PCB manufacturing. In 2022, the company’s consolidated revenue exceeded 1.99 billion USD, reflecting its strong market position and financial stability. Tripod continues to invest in next-generation manufacturing processes, cutting-edge equipment, and sustainable business practices to drive long-term growth. By combining advanced technology, manufacturing expertise, and a commitment to excellence, Tripod Technology Corporation remains at the forefront of the global PCB industry, shaping the future of electronics and clean energy solutions.
About Tripod Nanotechnology Corporation
Originating from a chemical research division within Tripod Technology Corporation, Tripod Nanotechnology Corporation specializes in noble metal electroplating, precious metal recycling solutions, and the production and application of nanomaterials. Established in 2018, Tripod Nanotechnology has been recognized with the National Innovation Award for three consecutive years and holds multiple patents across Australia, Germany, Japan, Taiwan, the UK, and the United States.
Tripod Nanotechnology is a pioneer in hydrogen energy and biomedical applications, offering advanced PEM membrane electrodes, PEM electrolyzer, and nanomaterials for medical diagnostics and antimicrobial purposes. The company is also deeply committed to ESG and Circular Economy principles, pioneering noble metal recycling technologies and sustainable solutions for PCB dust recovery and reuse. With a strong foundation in material science innovation, Tripod Nanotechnology tailors its solutions to different manufacturing processes, enhancing product value and sustainability across industries.
New £1.5M UK-Taiwan Initiative Targets Next-Gen Hydrogen Production
New £1.5M UK-Taiwan Initiative Targets Next-Gen Hydrogen Production - Fuelcellsworks
UK cleantech specialist Bramble Energy partners with Taiwan firms to develop affordable, scalable hydrogen production technology through a £1.5m project.
fuelcellsworks.com
'Fuel Cell' 카테고리의 다른 글
이슈 진단 ① 위기 속 건물용 연료전지산업 살리자 (0) | 2025.04.14 |
---|---|
K-수소 아이콘, 디 올 뉴 넥쏘로 새출발 (2) | 2025.04.11 |
Trump pardons Trevor Milton, founder of bankrupt truck maker Nikola convicted of fraud (0) | 2025.03.31 |
「エネファーム」不適切販売 顧客に偽データ提示 大阪ガス子会社 (0) | 2025.03.31 |
Advent Technologies receives Go-Ahead from Airbus for Phase Two of Joint Benchmarking Project (0) | 2025.03.27 |